Maintaining a steel building workshop is crucial for ensuring its longevity, safety, and functionality. Regular maintenance can prevent costly repairs, enhance the building’s performance, and keep it in compliance with safety regulations. This guide outlines the steps and best practices for maintaining a steel building workshop effectively.
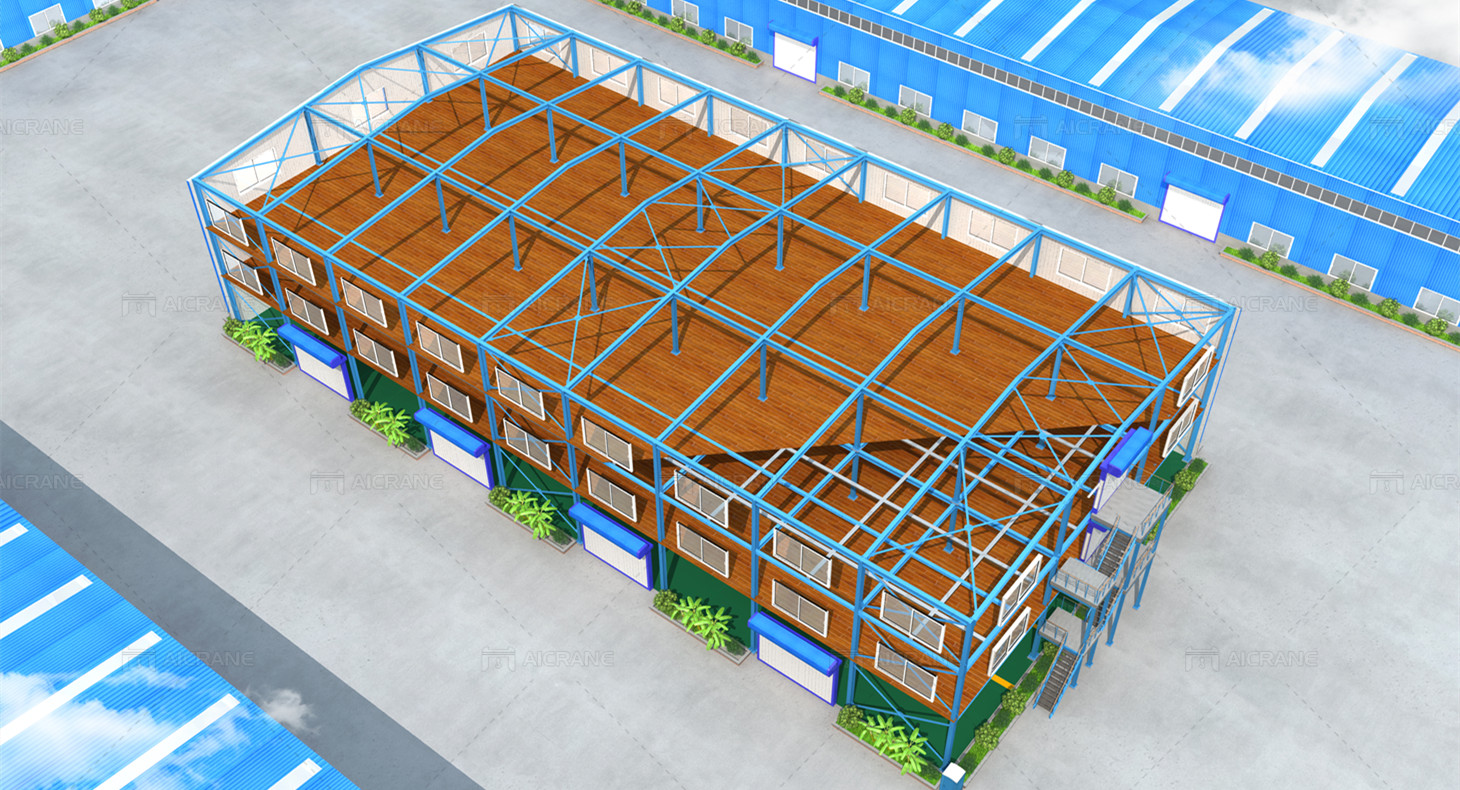
Routine Inspections
Exterior Inspections
Regular exterior inspections are essential to identify and address potential issues before they become major problems. Key areas to inspect include:
Roof: Check for signs of corrosion, loose panels, and debris accumulation. Ensure that the roof’s drainage systems, such as gutters and downspouts, are functioning correctly to prevent water buildup.
Walls: Look for dents, scratches, or signs of rust on the steel panels. Pay attention to areas around windows and doors, as these can be susceptible to leaks and damage.
Foundation: Inspect the foundation for cracks or settling, which can compromise the structural integrity of the building. Ensure that the foundation remains level and stable.
Interior Inspections
The interior of the steel building also requires regular checks to maintain its structural integrity and safety. Focus on the following areas:
Framing: Examine the steel framing for any signs of rust, corrosion, or damage. Ensure that all bolts and connections are secure.
Insulation: Check the insulation for moisture, mold, or damage. Proper insulation is crucial for maintaining energy efficiency and preventing condensation issues.
Electrical Systems: Inspect wiring, outlets, and lighting fixtures for signs of wear or damage. Ensure that all electrical systems comply with safety standards and function correctly.
Mechanical Systems: If the workshop is equipped with HVAC systems, machinery, or other mechanical systems, ensure they are regularly serviced and maintained according to the manufacturer’s recommendations.
Cleaning and Maintenance
Regular Cleaning
Keeping the workshop clean is vital for preventing damage and ensuring a safe working environment. Regular cleaning tasks include:
Roof and Gutters: Remove leaves, dirt, and other debris from the roof and gutters to prevent water buildup and corrosion. Check for and repair any leaks or damaged areas promptly.
Walls and Windows: Clean the exterior and interior walls with a mild detergent to remove dirt and grime. Clean windows of steel structure warehouse to ensure maximum light penetration and visibility.
Floors: Sweep and mop the floors regularly to prevent dust and debris buildup. For concrete floors, consider sealing them to prevent staining and damage.
Rust Prevention and Treatment
Rust is a common issue in steel buildings, especially in humid or coastal environments. To prevent and treat rust:
Protective Coatings: Apply a protective coating or paint to the steel surfaces of steel structure to prevent rust. Ensure that the coating is compatible with the building’s environment and is reapplied as needed.
Rust Removal: If rust spots are detected, clean them immediately using a wire brush or sandpaper. Apply a rust inhibitor and repaint the area to prevent further corrosion.
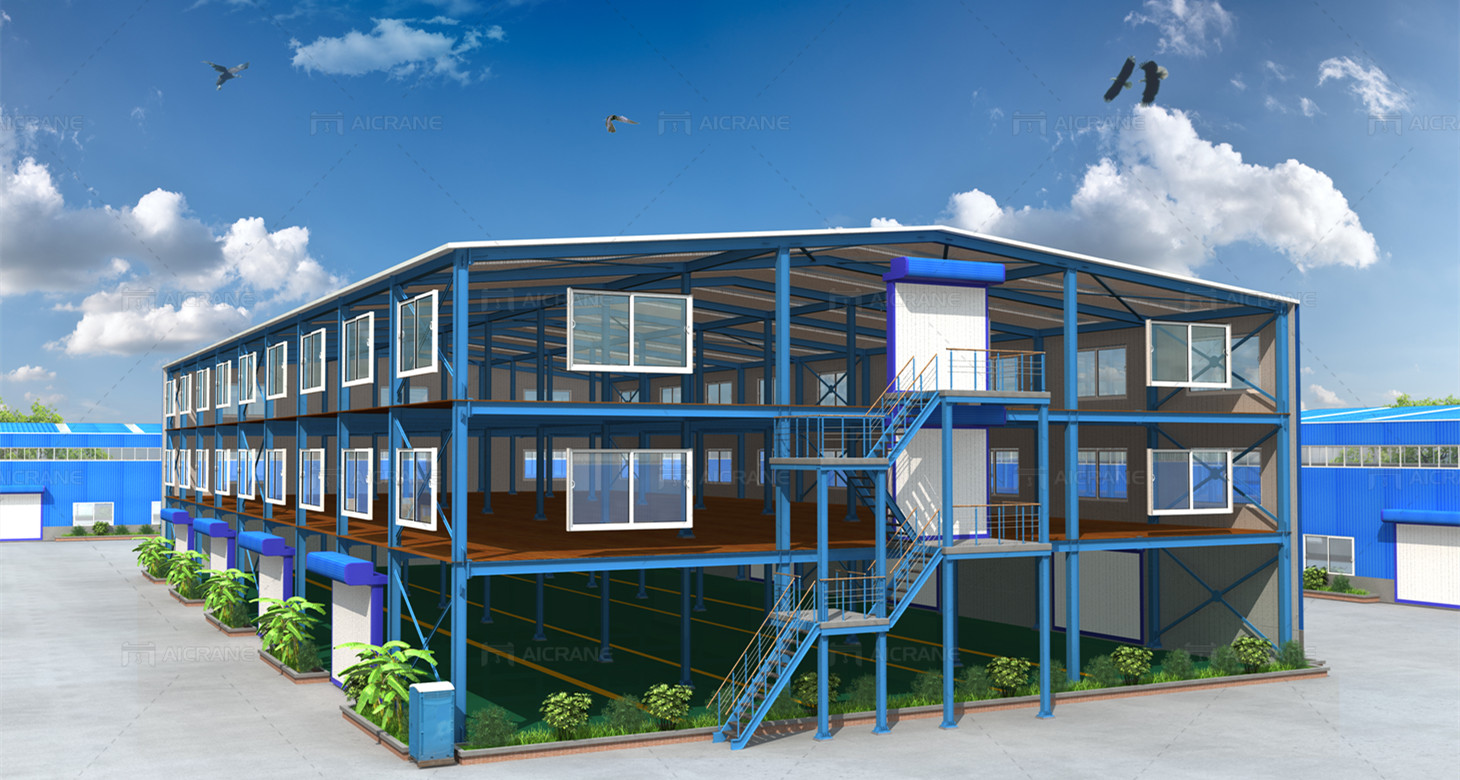
Structural Maintenance
Repairs and Replacements
Addressing minor issues promptly can prevent them from becoming significant problems. Regularly check for:
Loose or Damaged Panels: Tighten any loose screws or bolts and replace damaged panels immediately. Ensure that replacements match the original specifications.
Sealants and Caulking: Inspect sealants around windows, doors, and joints. Replace any cracked or deteriorating sealants to maintain the building’s waterproof integrity.
Doors and Windows: Ensure that doors and windows open and close properly. Lubricate hinges and locks, and replace any damaged components.
HVAC and Plumbing Systems
If the workshop includes HVAC or plumbing systems, regular maintenance is essential:
HVAC Systems: Change filters regularly, clean ducts, and have the system inspected by a professional at least once a year. Ensure that the system operates efficiently and maintains a comfortable working environment.
Plumbing: Check for leaks, drips, or signs of water damage around sinks, bathrooms, and other plumbing fixtures. Address any issues promptly to prevent water damage and mold growth.
Safety and Compliance
Fire Safety
Maintaining fire safety systems is crucial for protecting the workshop and its occupants:
Fire Extinguishers: Ensure that fire extinguishers are accessible, properly charged, and inspected regularly. Train employees on how to use them.
Sprinkler Systems: If the building has a sprinkler system, have it inspected and tested annually to ensure it functions correctly.
Emergency Exits: Ensure that all emergency exits are clearly marked and free of obstructions. Conduct regular fire drills to familiarize employees with evacuation procedures.
Regulatory Compliance
Adhering to local building codes and regulations is essential for legal and safety reasons:
Inspections: Schedule regular inspections with local authorities to ensure compliance with building codes and safety regulations.
Documentation: Keep detailed records of all maintenance activities, inspections, and repairs. This documentation can be crucial for regulatory compliance and insurance purposes.
Long-Term Considerations
Upgrades and Improvements
As the workshop ages, consider making upgrades and improvements to enhance its functionality and efficiency, you can contact the manufacturer for more information:
Energy Efficiency: Implement energy-efficient lighting, insulation, and HVAC systems to reduce operational costs and environmental impact.
Technology: Integrate modern technology, such as automated systems and smart controls, to improve productivity and safety.
Expansion: If the workshop needs to expand, plan the expansion carefully to ensure it integrates seamlessly with the existing structure and meets future needs.
Maintaining a steel building workshop involves a combination of regular inspections, cleaning, repairs, and upgrades. By following these best practices, you can ensure that your workshop remains safe, efficient, and in excellent condition for years to come. Proper maintenance not only extends the lifespan of the building but also enhances its functionality, providing a safe and productive environment for all users.